Overview
The rate of technological advancement has never been faster in the history of mankind than it is now. It is no less difficult for paper mills to stay up to date with technical advancements, which requires a significant capital commitment, qualified people resources, and, most importantly, a vision.
The company is extremely proud of its capacity to implement cutting-edge technologies in the fields of process, environment, energy and water conservation, plant maintenance, product development, and system development.

Plant Information
Management System (PIMS)
The world around us has been changing on a daily basis along with the development of human civilization. Therefore,the technological developments of production are changing as well. Industry 4.0 is a model that shows how industrial production follows the latest developments and changes over time. Thereby, the man, machine, and the production comes together as one intelligent and independent network.
Towards the direction of industry 4.0 and future development , we have implemented PIMS (Plant information management system) in the plant. These applications of new technology based on cyber-physical systems and the internet have led to significant improvements, such as an increase of automation, shorten intercommunication times, shortened periods between the development of new products and its market launch.
DCS-based Biomethanantion plant from Hydrothane (Netherland)
Effluent from Bagasse wet bulk storage and wet washing is treated in the Biomethanation plant before going to ETP and the recovered Biogas is used as a fuel in the boiler. COD reduction – 80% and BOD reduction – 90%
Sludge Dewatering Press by BALLMER.
Effluent from primary treatment contains solids/ short fiber which are removed by Sludge Dewatering press thereby ensuring the dryness of 45% which helps the removed solids compatible to be used as fuel for the boiler.
Wood Pulping and ClO2 Bleaching
Mixed hard wood-based fiber line of daily pulp production 300 TPD commissioned in 4th quarter of 2021. It is equipped with the most advanced technology to produce quality bleach pulp with minimum impact on the environment.
The essential features of the Opti batch – C cooking plant, two-stage oxygen delignification, and ICF bleaching are to generate high yield pulp in an odor-free environment.
Pulp washing is performed using high-efficiency wash presses, which cut water consumption by half compared to traditional washers and contribute less COD to effluent.
9.0 TPD Chlorine dioxide is based on R6 technology supplied by a renowned technology supplier with world-class safety standards. R6 technology produces ClO2 without the use of hazardous chemicals, with zero discharge and no emission of toxic gases.


Recovery Boiler
High-Efficiency Recovery Boiler (HERB-RB) 550TDS firing commissioned in 2021. to recover Pulping chemical and heat energy, Its Chemical Recovery Efficiency is more than 96.0 %, and also able by-products to generate 10.2 MWh Power and Steam for the process used.
ESP for recovery boiler
To make the Environment safe we used the best technology, Electrostatic Precipitator (ESP) which Performed well and maintained <30 PPM emission in Recovery Boiler Stack. To make Operation Efficient and equipment safe we are using Safety Related System (SRS) on Recovery Boiler.

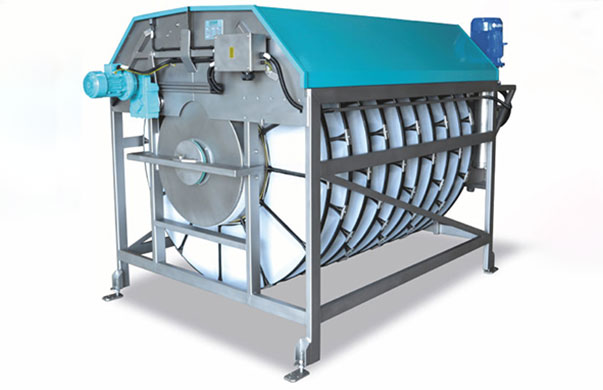
Opti Disc Filter
To produce White Liquor used Opti Disc Filter which is the best technology to convert Green liquor to White liquor with a conversion efficiency of more than 93.0 %. And it helps to minimize the chemical loss in the system.
Lime Sludge Reburning Kiln
To Make the Environment safe. We commissioned the Latest technology Rotary Lime Kiln with a Capacity of 200 TPD to convert Lime mud (Calcium Carbonate/CaCO3) to Lime (Calcium Oxide/CaO).BMS (Burner management system) technology is used in Rotary Lime Kiln to best utilized fuel efficiency and made safe operation on the shop floor.
